How to choose a crusher, what can be used for reference?
How to choose a crusher for production is something that customers have always wanted to know when choosing a crusher. When choosing a crusher, they should consider the characteristics of the material itself, such as the type and hardness of the material, the water content, the degree of splitting, the size of the material in and out, the construction site and the output.
1. Material type and hardness
Material type and hardness are important principles for selecting a crusher. The hardness of different materials is different, and the hardness of materials is usually expressed by Mohs hardness. The molar hardness is divided into 10 grades. The greater the molar hardness, the more difficult it is to crush the ore, and vice versa.
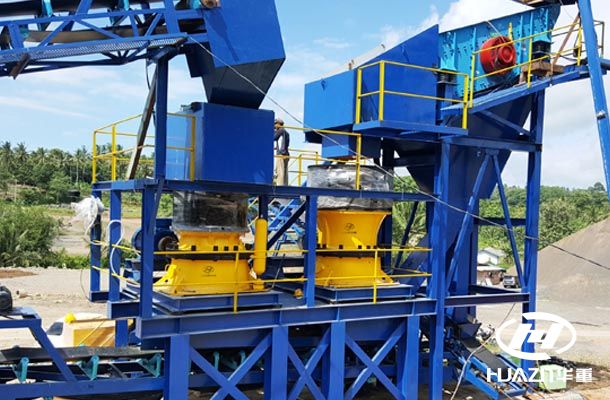
2. Moisture content of the material
The water content of the material will also affect the choice of crusher. When the moisture content is too large, due to the increase of humidity, the fine-grained materials will agglomerate or stick to the coarse-grained materials, thereby increasing the viscosity of the materials, reducing the drainage speed of the ore, and reducing the production efficiency. If the situation is serious, it will even cause the drain to be blocked and affect normal production.
3. Structural density of materials
The degree of structural density of the material also directly affects the productivity of the crusher-when the ore is crushed, it is easy to break along the cleavage surface. Therefore, the productivity of crushed ore with developed cleavage is much higher than that of ore with dense crushing structure.
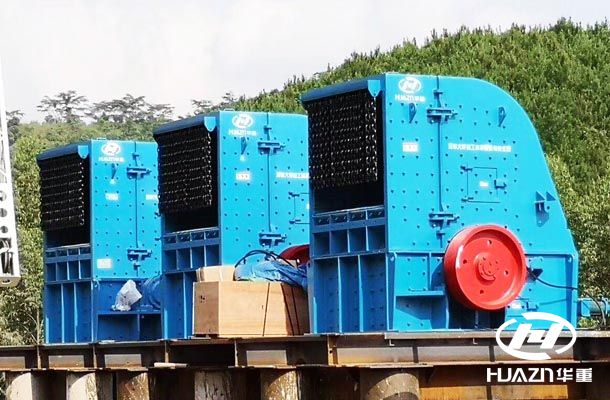
4. Particle size of feed and discharge
The particle size of the feed and discharge is used to determine the type of comminution equipment required and the degree of comminution.
If the content of coarse particles (large dry discharge mouth size) in the crushed material is high, or the ratio of the maximum feed block to the feed width is large, the crusher needs to achieve a larger crushing ratio (the ratio of the particle size of the material before crushing to the particle size of the material after crushing). Therefore, the production efficiency is reduced. If the fine particle content of the crushed material (close to or less than the size of the discharge port) is large, or the ratio of the maximum feed block to the feed width is small, the crushing ratio to be achieved is small, and the production rate of the crushed material should be increased accordingly.
5. Broken work site
The construction site area is also one of the factors that people should consider when choosing a crusher. In addition, the location of the crushing equipment will also affect the choice of crusher.
6. Production capacity
Production capacity is also an important indicator to determine the selection of crushing equipment. The traditional understanding is that the higher the output requirement, the larger the required size of the crushing equipment, and the corresponding input and output will increase.
Related Blog
Application Case of Electrical Control Cabinet Technology in Hydraulic Engineering
2025-06-26
Water conservancy projects, a term that may sound somewhat complex, are actually closely related to our lives. Imagine a dry summer, where the water in the reservoir can continuously supply the city's water needs; this relies on advanced electrical control cabinet technology. So, what exactly is an electrical control cabinet, and what important role does it play in water conservancy projects? What is an electrical control cabinet? Simply put, an electrical control cabinet is a device that integrates electrical control and protection, used to manage and control various equipment in water conservancy projects. Like a mysterious "brain," it processes various complex signals and data to ensure the efficient operation of water conservancy facilities. Whether it's the starting and stopping of water pumps or the monitoring of water levels, the electrical control cabinet plays a key role. Application of electrical control cabinets in water pump control Imagine that water pumps are like the "heart" of a water conservancy project, and the electrical control cabinet is its "brain." During the starting and stopping of the water pump, the electrical control cabinet adjusts the working status of the water pump in real time by receiving data from the water level sensor. When the water level is too low, the electrical control cabinet automatically starts the water pump; when the water level reaches the set value, it closes the water pump in time to avoid wasting water resources. This kind of automated control not only improves the efficiency of water pump usage but also greatly reduces the need for manual intervention.
Mine intelligent hydraulic station: characteristics and advantages
2024-10-22
The intelligent hydraulic station of Luoyang Dahua Intelligent Technology Co., Ltd. is a kind of hydraulic equipment used in the mining industry.
Advantages of intelligent electric control cabinet
2024-10-16
The intelligent electric control cabinet can provide high-precision measurement data, reflect the power quality data in real time, and realize the real-time monitoring of the distribution system and the effective management of the operation quality.